Das Wasserrad der Zuger Säge wurde nach den Vorgaben aus dem Wasserbuch Bescheid neu erstellt. Dabei sind lediglich der Durchmesser und die Breite des Rades angegeben, sowie die Größe der Wasserrinne und die maximale Wassermenge. Aus dem Gebäude und dort einbetonierten Schrauben, war die Position der Wasserrad-Welle definiert.
Ausgehende von diesen Daten, wurde mit Hilfe alter und neuer Bücher die Rekonstruktion des damaligen Rades gestartet. Da vom alten Wasserrad nur noch die Aufnahmen übrig waren, mussten zuerst die ganzen Werte für das Wasserad berechnet werden. Vom Durchmesser des Radkranzes über die Menge der Schaufeln und deren richtiger Winkel bis hin zur Stärke der Radarme, wurde alles neu berechnet und dann in einem 3D Modell gezeichnet.
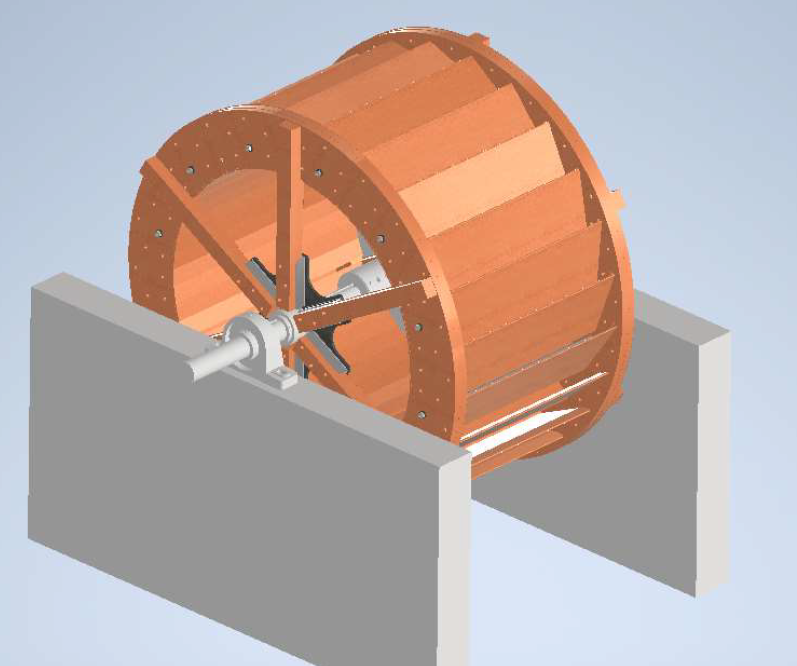
Das hier verwendete Wasserrad ist im Gegensatz zu den meisten gänigen Wasserrädern aber schon erheblich unterschiedlicht. Die meisten Wasserräder nutzen sehr wenig Gefälle, um das Wasser zum Rad zu bringen und dann wird ein möglichst großes Wasserrad genutzt um das Gewicht des Wassers für den Antrieb zu verwenden. Es wurde ein größtmöglicher Durchmesser angestrebt.
Das hier verbaute Wasserrad ist eine Sonderform, die nur im Gebirge vorkam. Hier wurde bei großem Höhenunterschied eine steile Rinne gebaut um den Stoß des Wassers zur Energieerzeugung zu nutzen. Dieses Rad wird auch als Stoßrad bezeichnet. Die Räder wurden dabei klein gehalten aber dafür eine große Drehzahl erreicht, mit dem Vorteil, dass man sich in der Säge eine Übersetzungsstufe sparen konnte.
Als Holz wurde eine in Lech gewachsene, engjährige Gebirgsfichte verwendet. Bei Mondzeichen Fische wurde das Holz gesägt und dann in weiteren Schritten nass verarbeitet und bis zum Zusammenbau immer feucht gehalten.
Vom Schneiden der Bretter bis zum fertigen Zusammenbau des Rades wurden ca. 300 Arbeitsstunden aufgewendet.
Die Aufnahmen der Streben und die Welle mussten neu angefertigt werden. Die Gusseisernen Aufnahmen vom alten Rad waren einmal komplett in 2 Teile bebrochen und bereits notdürftig repariert, und einmal bereits eingerissen aber noch nicht ganz durchgebrochen. Somit war es nicht mehr sinnvoll diese Teile wieder zu verwenden.

Zum Einbau war es notwendig, das Rad in zwei Hälften zu teilen, da sonst das Rad nicht als ganzen unter das Vordach eingebracht werden kann.
Der gesamte Radkranz wird nur durch Holznägel zusammen gehalten, die Schaufeln sind in den Radkranz eingesteckt. Gewindestangen halten die beiden Radkränze zusammen und die Arme sind mit dem Rad verschraubt. Außen wird das Rad durch ein Metallband am Umfang zusammengespannt.
Schwierig war auch die Fallkurve aus dem Gerinne in das Wasserrad zu treffen. Trotz Berechnungen war dies viel Arbeit um das Wasserrad “gut” zu treffen.
Wasserrad-gesamt-v7-DiagrammFür alle die sich für die genauen Details der Herstellung interessieren hier noch weitere technische Details und Infos. Mit hilfe verschiedener Bücher wurde versucht das Rad zu berechnen. Leider gibt es nur wenige Aufzeichnungen über Stoßräder. Und die Informationen die ich gefunden habe, waren zum Teil widersprüchlich, bis dahin, dass sich die Informationen gegenseitig ausschlossen. Und trotzdem musste ich irgendwie das Rad dann bauen. Hier alle gerechneten Teile mit Verweisen auf die verwendeten Formeln bzw. Bücher. Alle Verweise im folgenden Dokument beziehen sich auf das Buch Hölzerne Wasserräder von Herbert Jüttemann
Wasserrad-gesamt-v7-webAus diesen Berechnungen ergaben sich alle relevanten Daten um ein 3D Modell vom Wasserrad zu zeichen sowie für jedes Einzelteil Fertigungszeichnungen zu erstellen. Somit waren für jedes benötigte Bauteil alle technischen Details festgehalten und es konnte auch die Holzliste erstellt werden. Gebaut wurde das Wasserrad aus unserer sehr engjährigen, heimischen Fichte.
20200128-Wasserrad-Zuger-Saege-gesamt-komprimiert-ohne-BerechnungNach all der Vorbereitung der einzelnen Teile wurde das Rad dann fast fertig zusammen gebaut. Da es aus Platzgründen nicht möglich war das Rad als ganzes einzubauen, wurde das Rad so weit wie möglich montiert, vor Ort transportiert, dort in zwei Hälften geteilt und dann vor Ort fertig zusammengebaut. Damit es vor Ort mit den schweren Teilen keine Probleme gibt beim Zusammenbau, wurde ein Modell im Maßstab 1:10 angefertigt, um den Teilungsvorgang und den Zusammenbau zu “üben”. Hier wurde auch gleichzeitig kontrolliert ob alle technischen Zeichnungen stimmen. Die Teile wurden nach den Zeichnungen gelasert. Somit konnten dann auch die Schablonen für die Produktion der Teile im originalen Maßstab gelasert werden um dann auf der Kopierfräse die runden Teile zu produzieren.